Context: MECH_ENG 340-2 is a class where we CAD two molds, CNC machine them out of aluminum blocks, and injection-mold plastic parts.
Problem Statement: How might we manufacture injection molds to create plastic parts of acceptable quality?
Outcome: My team chose to do a wordplay on our Professor's name- Michael Beltran- which became MyKale Belltrain: a train with a bell, pulling a cart of kale.
Skills: CAD, CAM, CNC Milling, Injection Molding
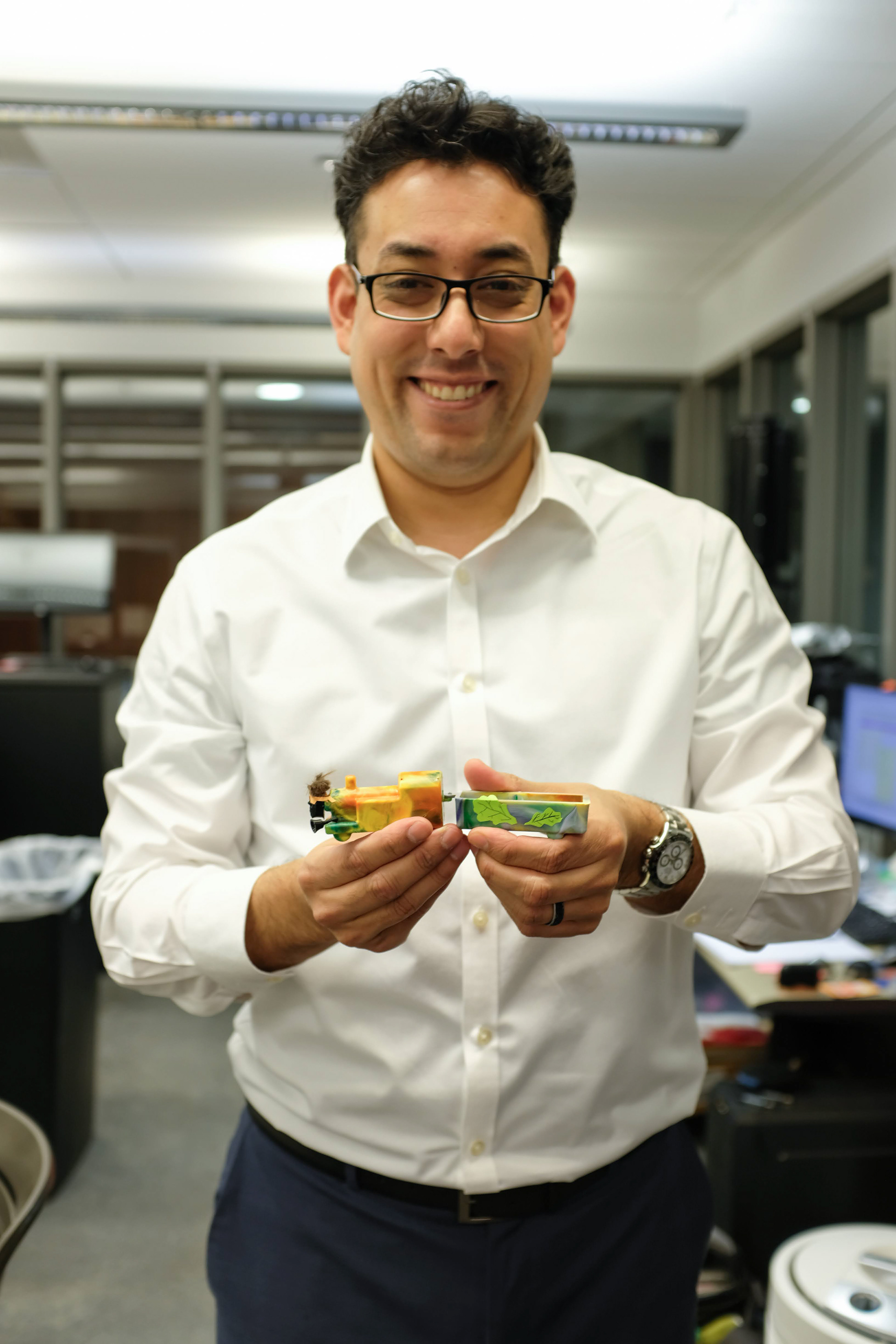
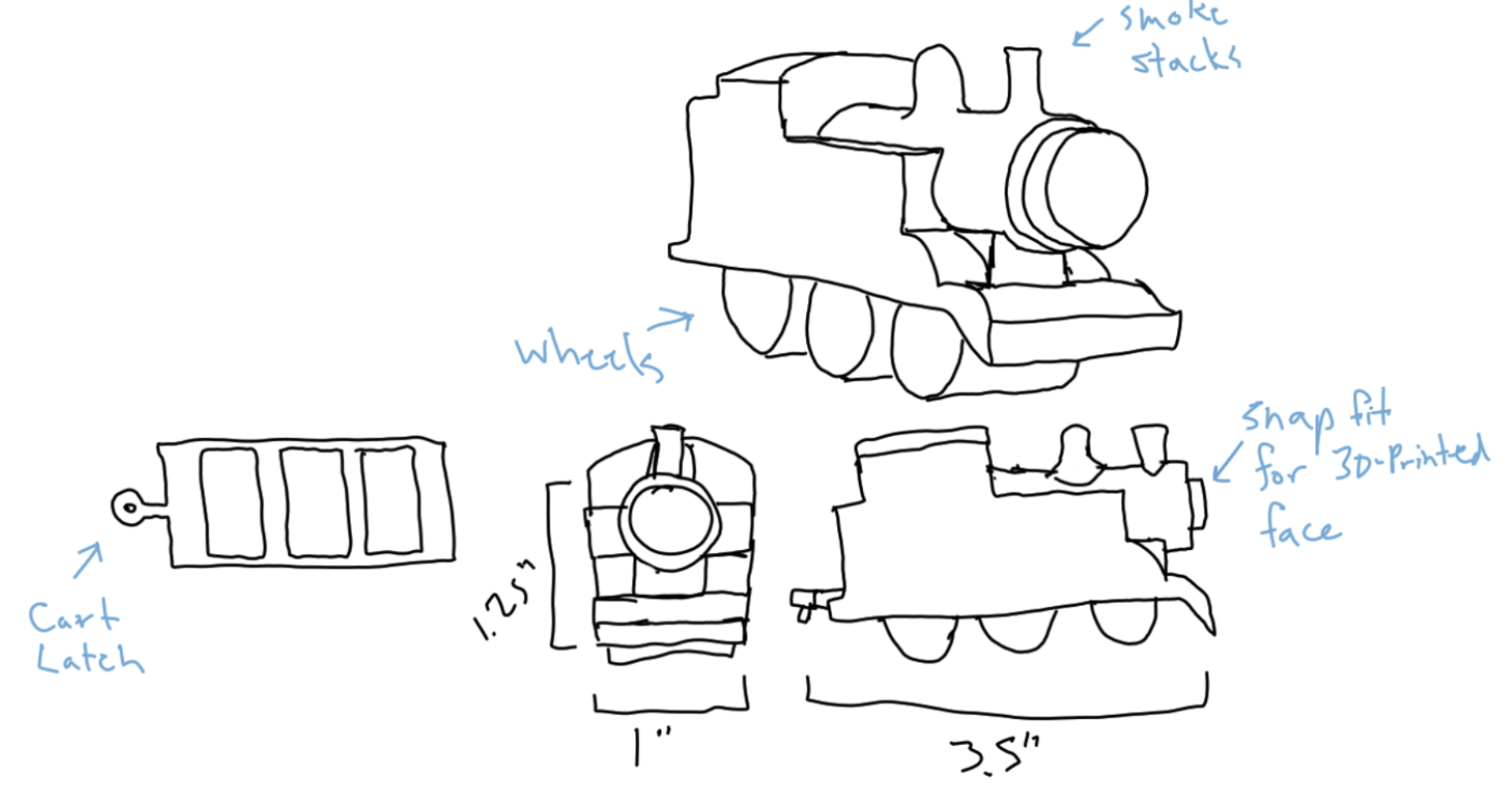
We first sketched out our idea with dimensions to fit the aluminum blocks to envision what MyKale Belltrain would look like.
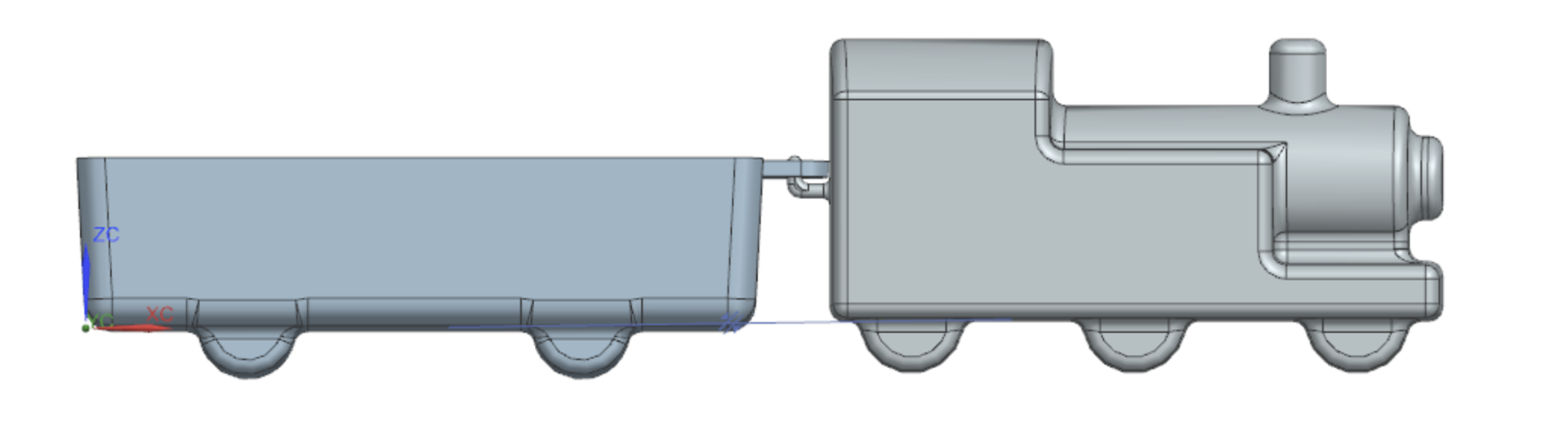
Adjustments had to be made when CAD-ing the model by removing features which would prohibit removal of the part from the mold. We also drafted all of the walls and calculated the size of our holes used for a pin-and-hole connection system to join two halves together.
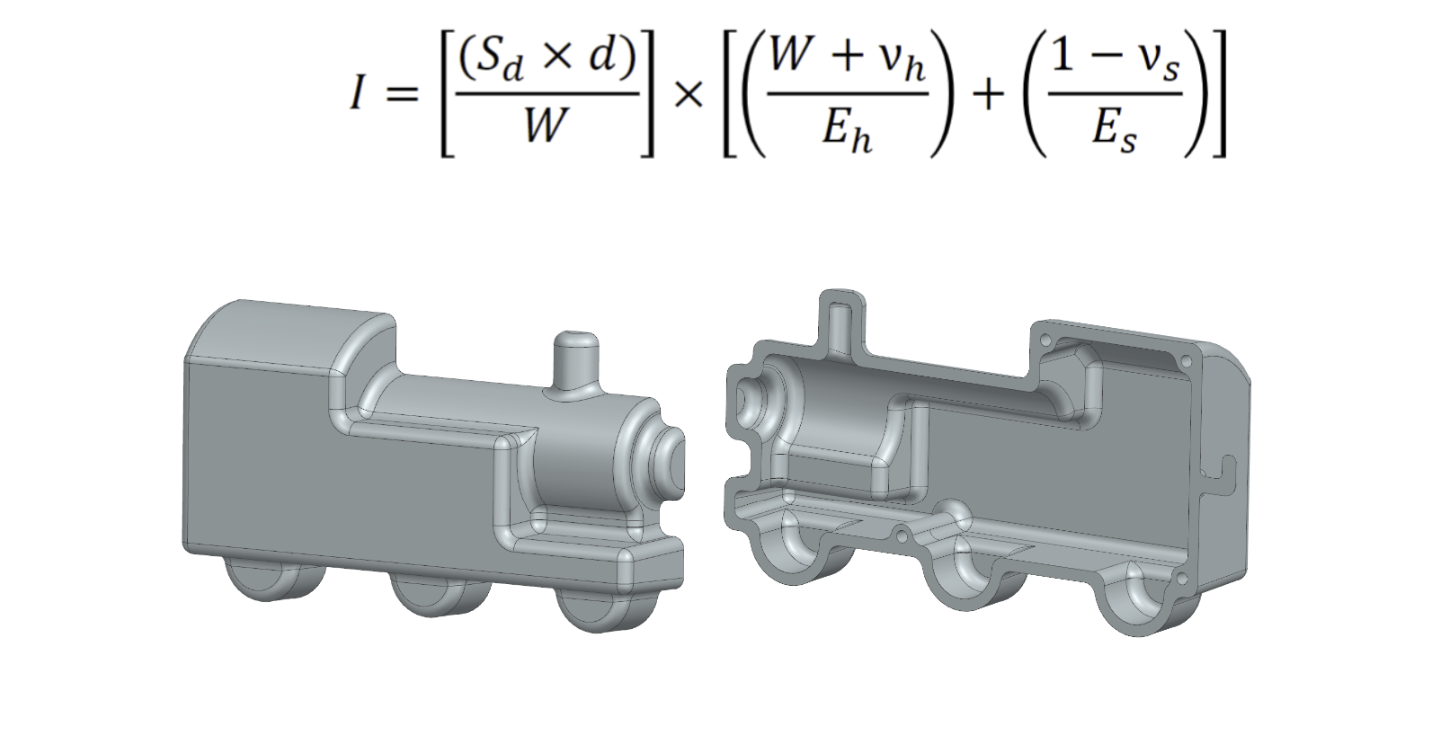
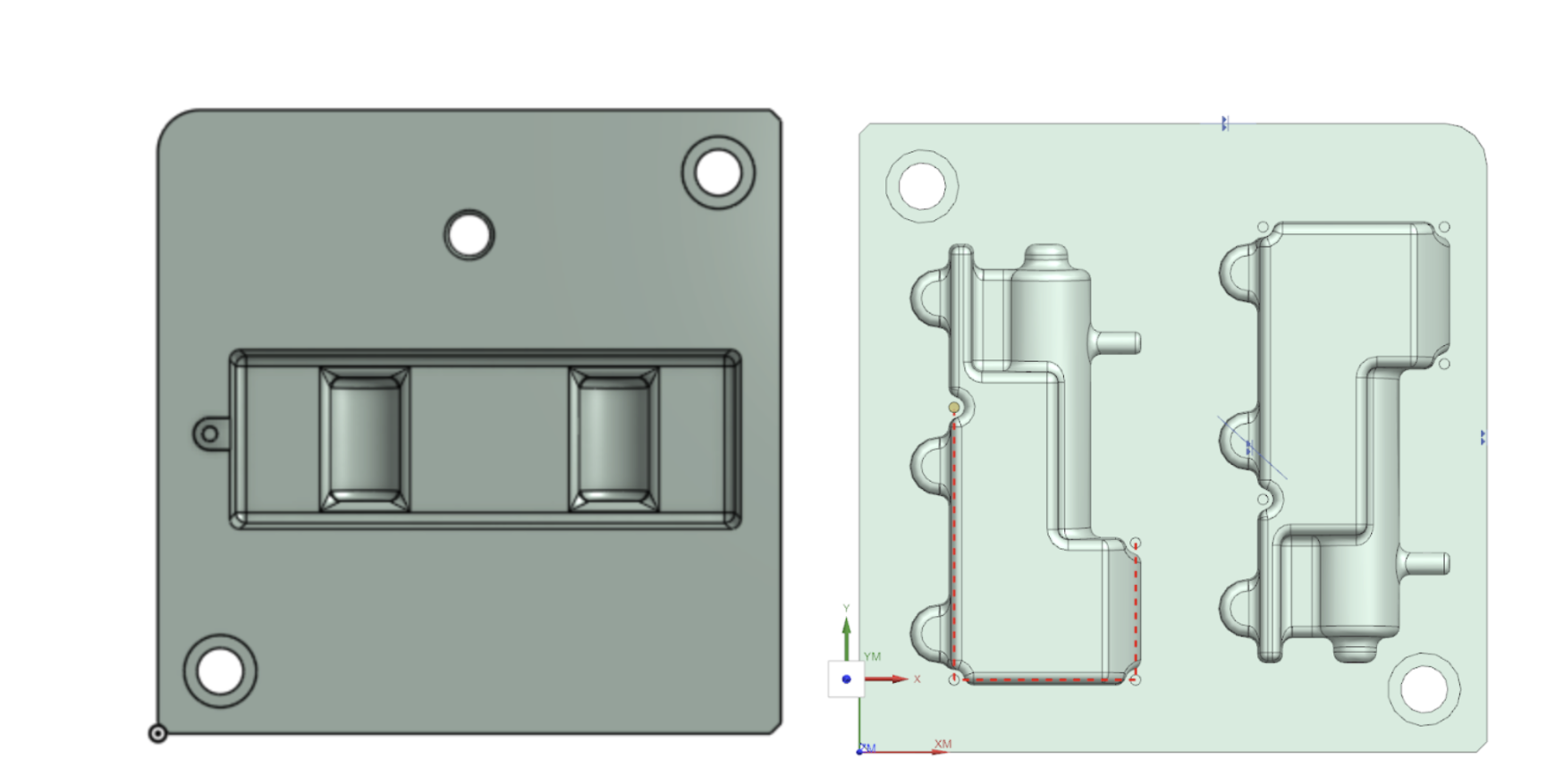
Once the CAD models were complete we created a cavity and core mold of both the train and the cart within CAD.
Once the molds were finished in CAD, we created CAM programs for each cavity and core mold. We looked at whether to use a ball mill or end mill, what the right type of operation would be, and how we could most reduce the operation time.
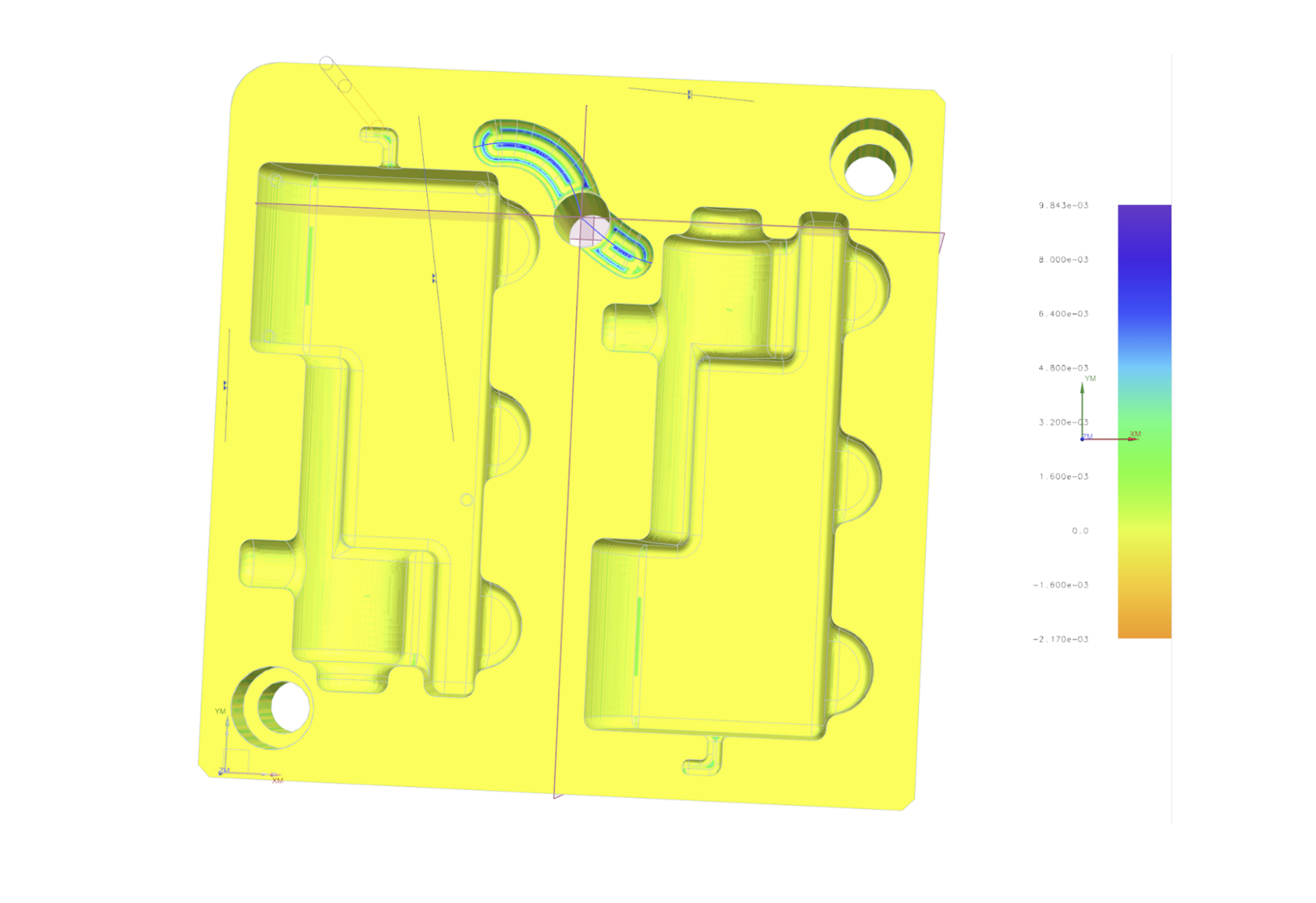
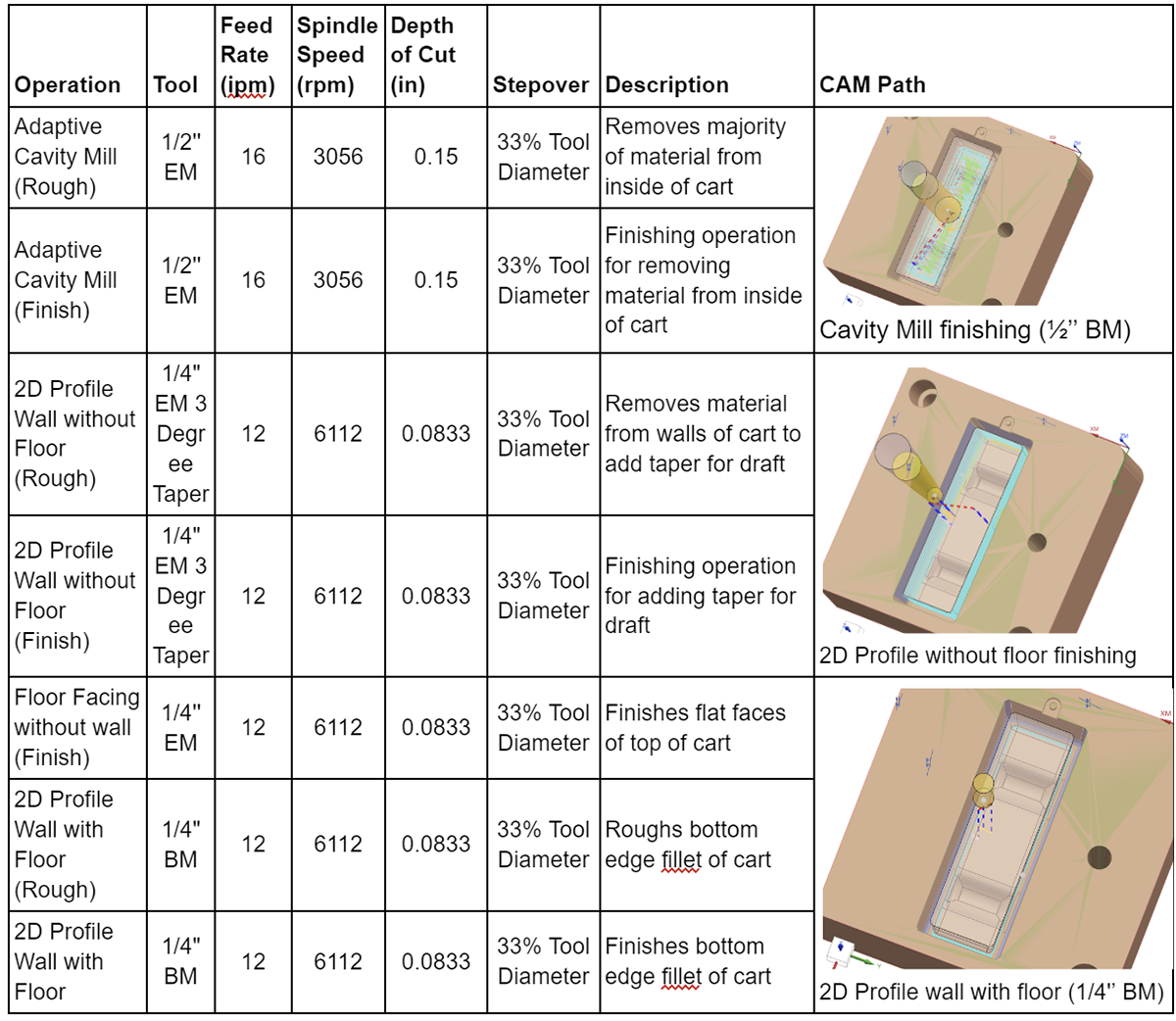
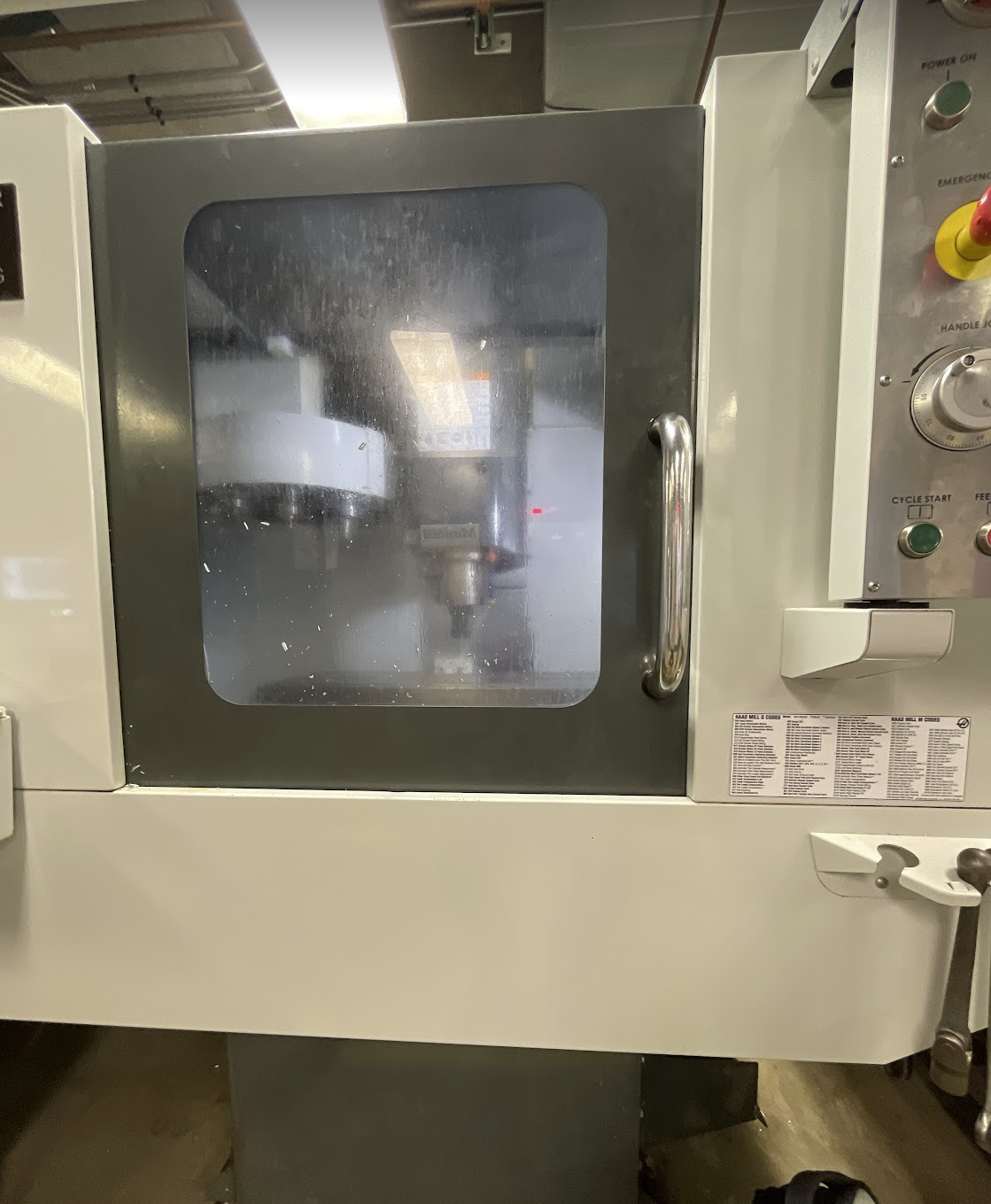
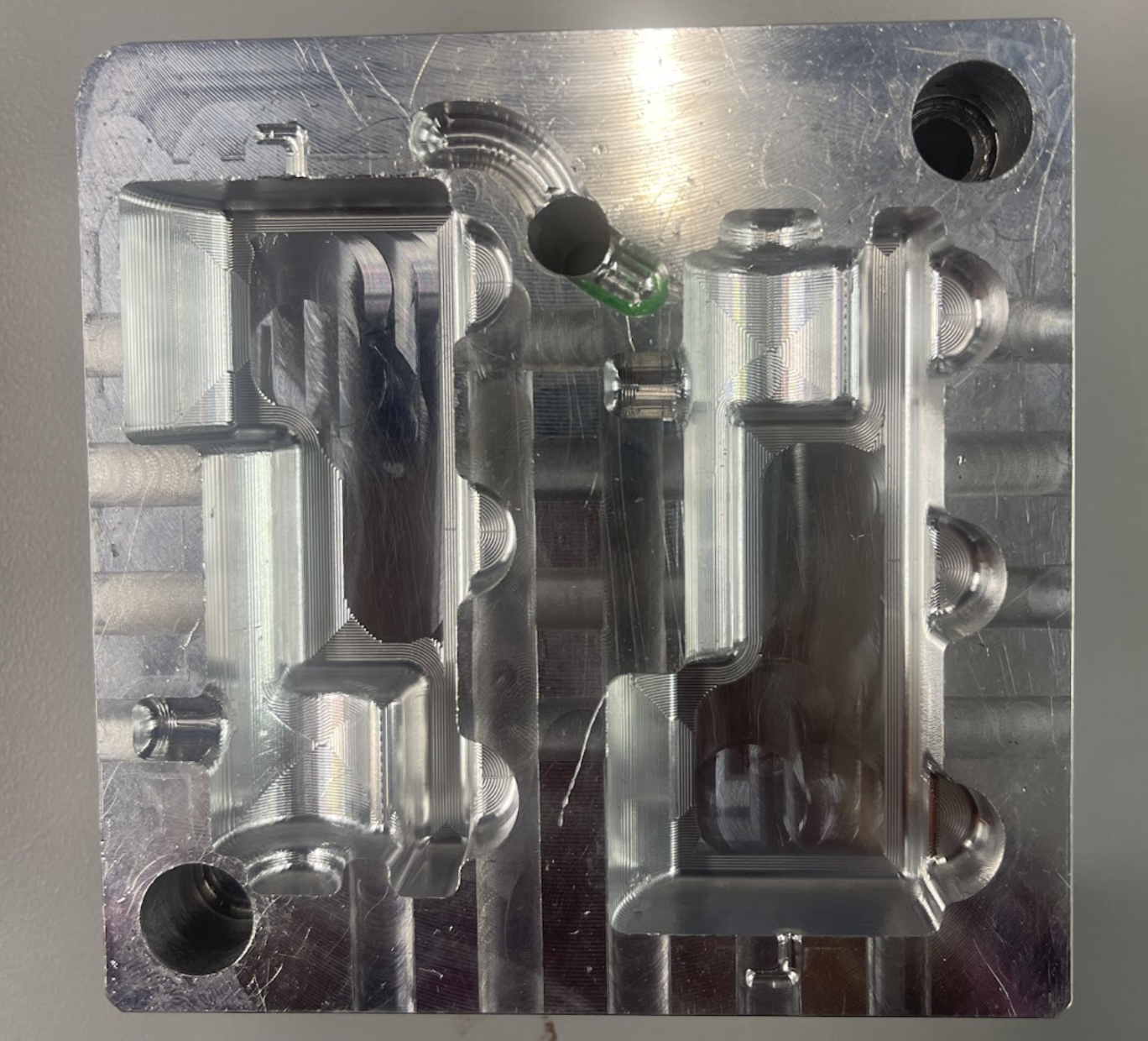
We then used Haas milling machines to mill our molds out of aluminum.
Lastly we installed our molds into the injection molding machines and learned how to change the press time, temperature, and air pressure to avoid short-shot and flash when injection-molding plastic.
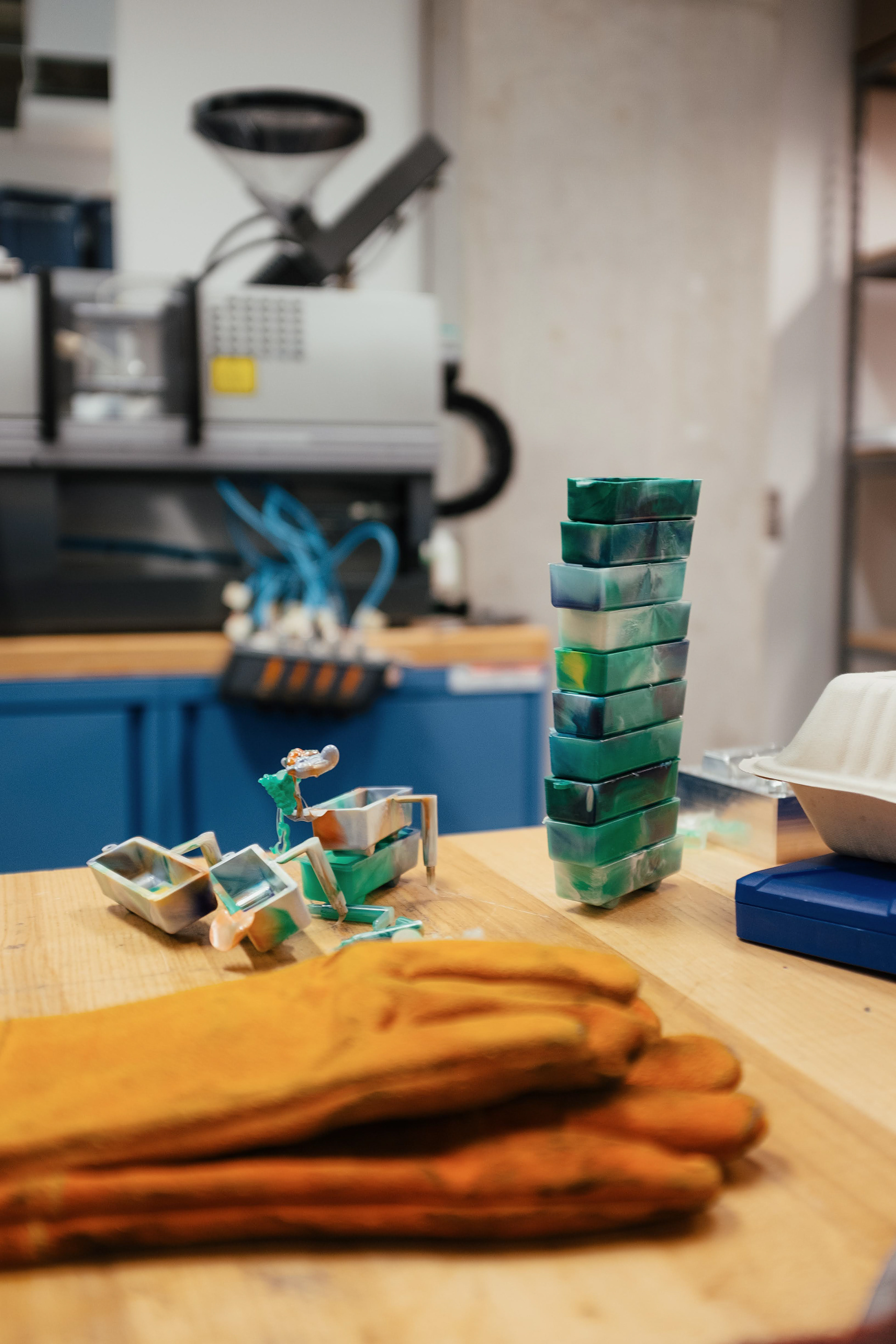
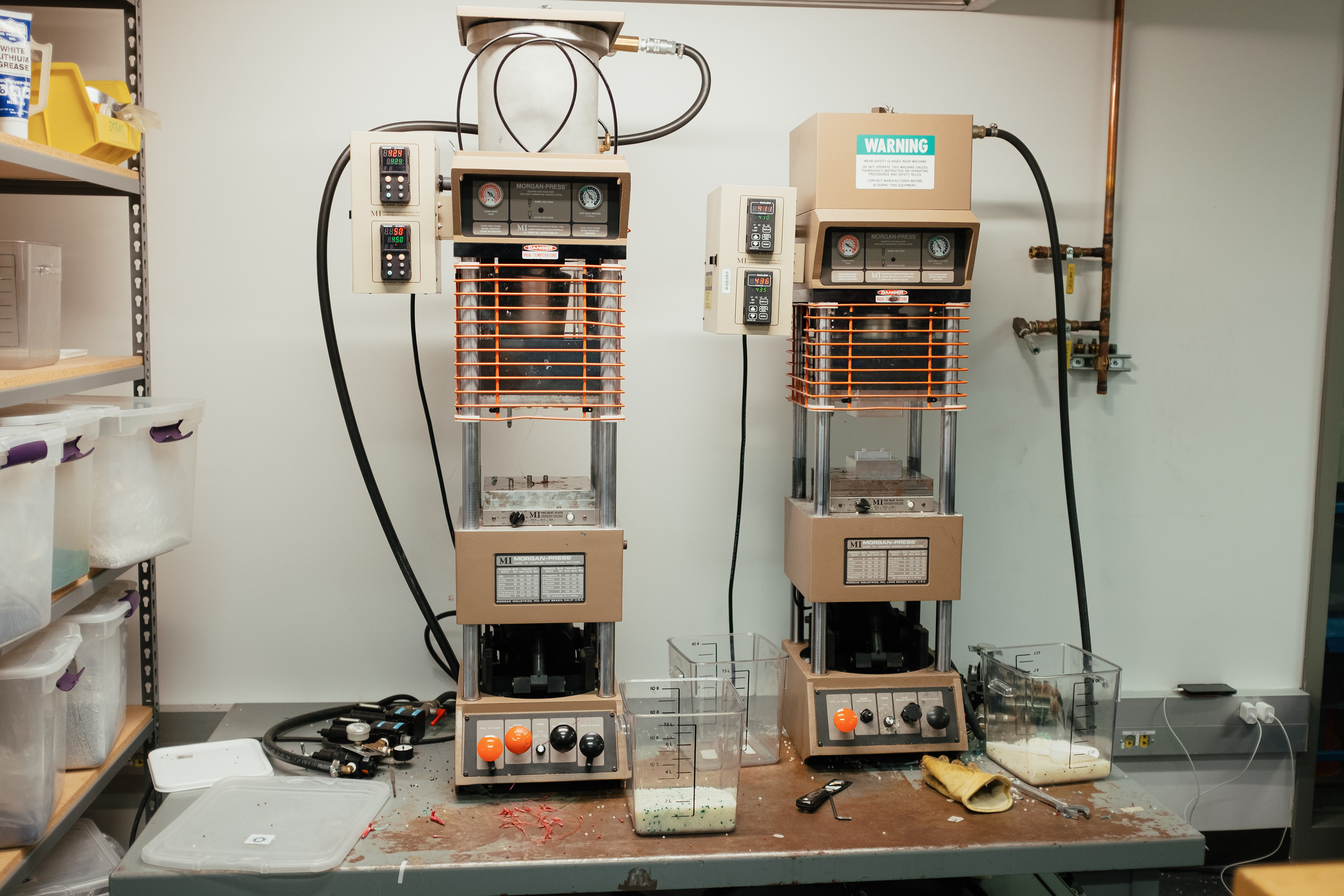